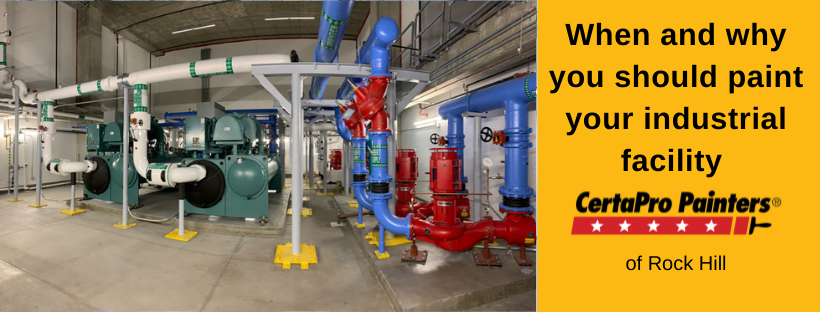
When and why you should paint your warehouse or industrial facility
Posted on August 2, 2021
Most people understand painting as a way to make their home look nice inside and out but in a commercial or industrial setting paint’s performance is about more than appearances.
In warehouses, factories and industrial settings paint also serves as part of the facility’s safety system and as a means of protecting equipment and infrastructure from damage.
Paint in these locations can be found on the floors, walls, equipment, and elsewhere. In many cases the paints are actually formulated to industrial strength standards in order to survive in harsh environments and to withstand a level of abuse no ordinary house paint could hope to.
Paint as “safety equipment”
Paint is used in industrial settings to mark off pathways, traffic flow, areas of physical danger, electrical and fire hazards, fire and safety equipment, exits, and internal operational areas and boundaries.
When these painted markings are on the floor, they are subject to intense wear and tear. Where they serve to inform or direct personnel and traffic, they need to be legible and visible at all times. Many floor markings get degraded by not only foot traffic, but traffic from wheeled carts, forklifts, pallets, and other heavy equipment.
When these markings are degraded or become worn and faded, they increase the chance of accidents occurring. They also may have legal, regulatory, or insurance requirements that call for them to be in a high state of visibility and clarity at all times.
Maintaining these important indicators is best left to commercial painters who are familiar with the best coatings and application methods to ensure their longevity and in the process, your compliance with any requirements.
If you are currently using paper signs, tape, barriers, barrels, etc. to achieve the same results you should strongly consider replacing them with commercially painted indicators to make clear that the indicator functions being served are clearly intended to be permanent.
You may also consider painting to indicate the types of wiring, plumbing, and ventilation inside your facility. If you have a mix of fuel, water, chemical, or compressed air plumbing running throughout your building then color-coding them can improve both safety and maintenance.
Paint as inventory and equipment protection
For the overall protection of your facility and its contents start by reviewing the exterior of your building. For commercial buildings, it is critical to make sure there is no water penetration. Proper prep work to seal the building is critical before any painting job but ensuring its integrity over time is also important. Caulking and sealant failures can create hazardous conditions inside your facility with water penetration leading to the growth of mold and mildew which can impact air quality.
Severe damage can also lead to corrosion and insect or rodent infestation. For any facility that stores inventory, especially anything related to food or medical equipment, this type of problem can threaten your entire business.
If you are finding indications of mold growth, standing puddles of water, high internal humidity, or signs of insect or rodent infestation you should contact a commercial painter who can seal your building with caulking even if you choose not to completely repaint the exterior.
For your equipment, a protective layer of the correct coatings can increase the lifespan and protect against corrosion that can lead to eventual failure.
When you begin to see signs of corrosion and rust forming on mission-critical equipment you should again consider contacting a commercial painter to protector your investment from water or chemical damage.
Your first steps
As a building owner, facility manager, or designated safety officer you should familiarize yourself with the marking and safety signage requirements for your facility. Inspect the existing quality of those markings and determine if any are missing or no longer clearly legible.
You should also consider painting internal plumbing, HVAC, and electrical systems to more clearly indicate the purpose, flow direction, and contents of each of them for safety, maintenance, and troubleshooting purposes.
Ensure that your facility is well sealed from the elements to prevent air, water, insect, and rodent infiltration. Inspect your equipment for rust and corrosion.
Finally
If your inspection efforts uncover problems in any of these areas feel free to contact CertaPro of Rock Hill for a free commercial painting estimate and consultation to learn what can be done to increase safety, compliance, and both facility and equipment longevity.